
INTEGRATED
SUPPLY CHAIN
END-TO-END IT STRATEGY FOR MODERN SUPPLY CHAIN
ACCENTIS has practical knowledge and experience in developing IT strategies for supply chain companies. We advise on completing the missing blocks in your solutions ecosystem, from selecting the right IT product to providing implementation and integration support. Our core expertise focuses on supply chain planning, logistics execution and supply chain transparency solution. We are a vendor-agnostic consulting company that integrates best-of-breed solutions. Depending on the project, we work either on the client side helping to scope, implement and roll-out the solution, or on the vendor side as an implementation partner.
SOLID SUPPLY CHAIN FOUNDATION
Efficient automation solutions combine lean logistics flows with lean IT flows, requiring a solid IT foundation. We integrate advanced IT systems to streamline supply chain execution workflows. ACCENTIS provides end-to-end support for your implementation project, from vision to go-live.


COMPLETE INTEGRATION PACKAGE
Efficient automation solutions combine lean logistics flows with lean IT flows, requiring a solid IT foundation. We integrate advanced IT systems to streamline supply chain execution workflows. ACCENTIS provides end-to-end support for your implementation project, from vision to go-live.
CORE MODEL
-
Develop an IT strategy
-
Gather business requirements
-
Select supply chain system
-
Create a TO-BE vision
-
Draft multi-system process logic
SOLUTION DESIGN
-
Conduct discovery workshops
-
Formalize business requirements
-
Adapt workflows to align with the TO-BE vision
-
Define change requirements
CONFIGURATION
-
Configure software
-
Clean master data
-
Ensure delivery of changes
-
Test the working prototype
-
Prepare training materials
IMPLEMENTATION
-
Perform technical deployment
-
Migrate master data
-
Conduct end-user training
-
Facilitate user acceptance tests
-
Deploy the solution
INTEGRATION
-
Integrate with automation equipment
-
Orchestrate multi-vendor automation
-
Optimize EDI and ETL processes
-
Implement AI solutions
PROJECT MANAGEMENT
-
Manage the project with vendors/clients
-
Supervise linked initiatives
-
Provide go-live support
-
Handle incident management and reporting
EXTENSIVE EXPERTISE IN SOLUTIONS
ACCENTIS consultants bring firsthand experience with leading supply chain solution providers and have actively contributed to their implementation projects. Here are just a few examples.

SUPPLY CHAIN PLANNING SOLUTIONS
SNM - SUPPLY CHAIN NETWORK MODELING
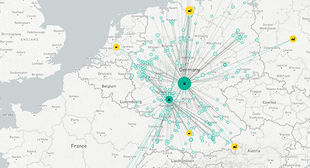
Supply Chain Network Modeling solutions are designed to enhance network efficiency and reduce operational costs. These tools enable businesses to simulate various scenarios, including demand fluctuations, capacity constraints, and transportation disruptions, ensuring more informed and strategic decision-making. Key functions include network optimization, inventory modeling, transportation analysis, cost-to-serve calculations, and risk assessment, providing data-driven insights to improve overall supply chain performance. Digital twin models help businesses identify bottlenecks, optimize resource allocation, and implement proactive adjustments to mitigate risks. These solutions are widely adopted across industries such as retail, manufacturing, pharmaceuticals, and logistics, enabling companies to build more resilient, agile, and cost-effective supply chain networks.
PLM - PRODUCT LIFECYCLE MANAGEMENT

A Product Lifecycle Management (PLM) system manages the entire product development process, from initial concept to end-of-life management. Key functions include collection planning, budgeting, product data management, and bill of materials (BOM) management, ensuring teams work with accurate, up-to-date information. By combining workflow automation and collaboration tools, PLM enhances cross-functional teamwork, accelerates time-to-market, and improves product quality. Its supplier collaboration and material sourcing capabilities help businesses track compliance, manage costs, and monitor sustainability metrics. Additionally, seamless integration with ERP, CAD, and other supply chain systems enhances visibility, efficiency, and data-driven decision-making.
ICBP - INTEGRATED COLLABORATIVE BUSINESS PLANNING
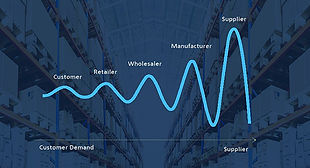
Integrated Collaborative Business Planning (ICBP) solutions enable organizations to align financial, operational, and supply chain planning on a single platform. These tools provide real-time scenario modeling, demand and supply planning, financial forecasting, and sales and operations planning (S&OP) to enhance decision-making, with a big focus on achieving collaborative arrangements, performance assessment and joint business plan. AI-driven analytics and predictive modeling help businesses anticipate market trends, optimize supply orders, supply planning, production and logistics planning while mitigating the bullwhip effect. Such tools require complex integration with ERP, WMS, MES, TMS, and other enterprise systems ensures data consistency and cross-functional collaboration.
F&R - DEMAND FORECAST & CONTINUOUS COLLABORATIVE REPLENISHMENT

Demand forecasting tools make use of AI & Machine learning to analyze historical sales data, seasonal trends, and external factors like promotions and economic shifts to predict future demand accurately.
Continuous replenishment solutions automate stock replenishment by dynamically adjusting order quantities based on real-time sales, inventory levels, and lead times, ensuring optimal stock availability in stores and warehouses. Key modules of these solutions include demand sensing, inventory optimization, supplier collaboration, and replenishment automation, helping retailers and supply chain companies reduce stockouts and minimize excess inventory. These solutions integrate with ERP for procurement data, WMS for inventory tracking, and POS systems to capture real-time sales data.
LOGISTICS EXECUTION SOLUTIONS
OMS - ORDER MANAGEMENT SYSTEM

An Order Management System (OMS) is an application that integrates orders from multiple channels, such as B2B sales, inter-site transfers, retail and e-commerce. It manages the entire order lifecycle, from order capture and processing to fulfillment and post-sales services, ensuring accuracy and efficiency. The system plays a key role in balancing inventory levels across various locations, reducing stockouts and overstock situations. By providing real-time visibility into inventory and order status, it enables supply chain companies to optimize their workflow and customer service. Additionally, the OMS is used to provide scalability and adaptability for modern supply chain ecosystem and meet the evolving demands of operations.
TMS - TRANSPORT MANAGEMENT SYSTEM
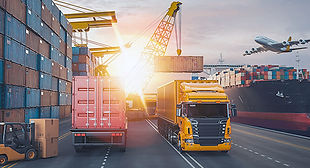
A Transport Management System (TMS) is software that optimizes the planning, execution, and tracking of transportation operations across supply chains. Key TMS functions include transport budget planning and control, contract management, load planning, carrier selection, route optimization, real-time shipment tracking, freight audit and payment, carrier performance tracking and analytics, fleet management, and connection to IoT gateways to capture information from devices and sensors enabling real-time fleet monitoring, including in-transit visibility of driving conditions, routes, and assets. It usually integrates with ERP, OMS, WMS, and external traceability systems to improve visibility and coordination across logistics networks.
YMS - YARD MANAGEMENT SYSTEM
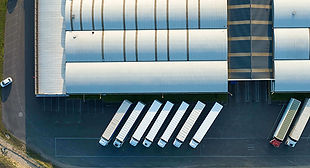
A Yard Management System (YMS) is a solution that optimizes vehicle traffic within a specific site. It provides access control at entrance gates, directs truck movements in the yard, assigns parking lots and manages waiting times. Additionally, it sends trailers to designated docks for loading and unloading processing. This solution ensures efficient planning of goods receiving and dispatch. Typical functions include:
-
Appointment planning and time-slot management for inbound and outbound trucks.
-
Capacity management for parking lots and docks. Synchronization of loading/unloading activities.
-
Driver notifications.
-
Collection of process timestamps for KPIs, reports and audits.
WMS - WAREHOUSE MANAGEMENT SYSTEM

A Warehouse Management System (WMS) is a software package that primarily handles warehouse activities such as goods receiving, put-away and replenishment, order picking and packing, shipping and manifesting, inventory management, and resource/labor management. This system is a central component for tracking the movement of logistic units, including pallets, cartons, boxes, and individual items, within a modern warehouse. It provides connectivity and facilitates information exchange with handheld scanners, printing peripherals, and other warehouse equipment. Additionally, it optimizes storage locations and picking routes. It also integrates with other supply chain systems, such as ERP, OMS, TMS...
WES - WAREHOUSE EXECUTION SYSTEM
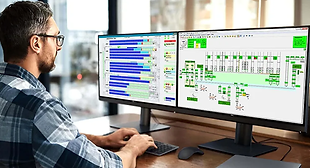
​A Warehouse Execution System (WES) is a solution that is deployed in highly automated systems. It is responsible for real-time coordination and prioritization of tasks, as well as the optimization of material handling workflow. It orchestrates order fulfillment, inventory management, and task allocation to various automated systems and human operators. It is used as a hub to connect multiple WMS solutions, multiple automation equipment (AS/RS, conveyor, AGV, robot) and multiple human interface devices (scanners, pick-to-light, put-to-light, scales...). This solution is particularly beneficial for companies that require seamless integration of multiple WMS packages with several WCS systems.
WCS - WAREHOUSE CONTROL SYSTEM

A Warehouse Control System (WCS) handles real-time equipment control, monitoring, visibility, routing, and optimization, ensuring the smooth and efficient movement of goods within an automated solution. It also provides interfaces between automation equipment and human interface devices. Depending on the context, the WCS acts as a bridge between either the Warehouse Management System (WMS) or the Warehouse Execution System (WES) and material handling equipment, translating high-level instructions into machine-level commands. A modern distribution center or production facility may have multiple WCS solutions from different equipment suppliers, working together to manage various islands of automation.
MES - MANUFACTURING EXECUTION SYSTEM
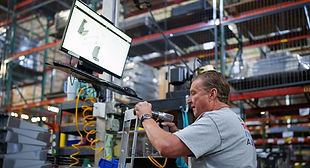
​A Manufacturing Execution System (MES) is software that monitors, tracks, and controls manufacturing processes in real time to enhance production efficiency and quality. It optimizes production workflows, minimizes downtime, and improves overall supply chain efficiency. Key MES functions include production scheduling, resource allocation, performance analysis, quality management, and real-time tracking of materials and work-in-progress. It connects shop floor equipment with ERP, WMS, or WES, ensuring seamless data synchronization between planning and execution. MES is widely used in industries such as automotive, pharmaceuticals, electronics, and food processing to enhance traceability, reduce waste, and ensure regulatory compliance.
SUPPLY CHAIN VISIBILITY AND EFFICIENCY
T&T - TRACK AND TRACE PORTAL
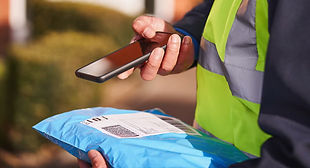
A typical Track & Trace portal consolidates traceability data from multiple sources across the supply chain, presenting it in a structured format that highlights key order status updates, due dates, and important checkpoints for parcel or logistics unit locations. A crucial aspect is managing planned versus actual timelines and milestones to ensure operational accuracy. The portal also includes notification and alert features to detect anomalies such as delays, stockouts, and unexpected order status changes. Additionally, it offers dashboards with performance metrics for enhanced visibility and decision-making. Key data providers typically include TMS, WMS, YMS, external carrier systems, customs clearance services, and other online tracking portals, all connected through pre-built connectors, APIs, and interfaces.
DPP - DIGITAL PRODUCT PASSPORT

A Digital Product Passport (DPP) ecosystem of connected solutions enables compliance with the European Union's sustainability initiatives. These systems require robust product data management and tracking of product movements across the entire supply chain throughout the product lifecycle. Integration with systems such as PLM, ERP, TMS, WMS, POS, external supplier platforms, and customs databases is essential. Powered by serialization, the DPP process enhances transparency and efficiency in supply chains, reducing the risk of counterfeiting, theft, and diversion—especially in industries like pharmaceuticals, food, electronics, fashion, and more. Key functions of a DPP solution include supplier product data management, digital ID management, labeling, serialization, authentication, and post-sales product lifecycle management, such as recycling, repair, and reuse.
BPM - BUSINESS PROCESS MODELING AND MINING

Business Process Modeling and Mapping tools enable the creation of visual representations of processes, helping to formalize workflows and identify optimization opportunities. Business Process Mining, on the other hand, gathers data from processes to analyze behaviors, deviations, anomalies, and inefficiencies. Our approach integrates both techniques to offer a clear and comprehensive view of process flows, revealing insights into actual performance and allowing for a comparison between the existing processes and the desired model. By combining these elements, we provide a complete and accurate picture of the business process, facilitating targeted improvements in efficiency and effectiveness.
KPI - REPORTING AND BI FOR SUPPLY CHAIN

A good KPI dashboard provides a clear picture of where your business stands. A specialized KPI cockpit centralizes data from WMS, TMS, ERP, and other systems, ensuring accurate tracking of operational efficiency, inventory levels, transportation performance, and order fulfillment. The cockpit utilizes industry-standard metrics such as Inventory Turnover Rate (ITR), Perfect Order Measurement (POM), Fill Rate (FR), Customer Order Cycle Time (COCT), Inventory Accuracy (IA), Backorder (BO), Supply Chain Cycle Time (SCCT), On-Time Delivery (OTD), In-Full Delivery (IFD), Pick and Pack Cycle Time (PPCT), Inventory Days of Supply (IDS), Days Sales of Inventory (DSI), Inventory Velocity (IV), Damage-Free Delivery (DFD), Storage Utilization in the Warehouse (SUW), Inventory Adjustments Made (IAM), and many more.